What's inside a professional cue?
- Rob Rice
- Jan 27, 2019
- 3 min read
Updated: Apr 20
You may be surprised to learn what goes into the making of a quality pool cue...

The first step in understanding the anatomy of your cue is knowing what type of cue you have. There is a huge difference between a "sticker cue" and a quality built custom cue. Here, I'm showing the most common way a custom cuemaker would build a cue from quality components. A sticker cue is the most common, and most, if not all, of the decorations are simple stickers stuck over a single tapered dowel of wood. These diagrams (stolen from Prather Cues) show in detail what's going on inside the custom cue.
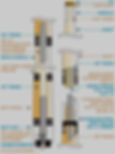
It is critical that each hole, tenon, rod, sleeve, etc. be perfectly concentric and mated precisely. A poorly made cue will lead to buzzes at impact, rattles, warping, cracking of the finish and breakage.
So why do we need all this hidden engineering?
Each piece of the cue has a special purpose, but the main goals a cuemaker is trying to achieve are...
Control the balance and the feel of the hit.
Control the wood's tendency to shrink and expand leading to warpage and cracking.
Make the cue look good!
First of all let's discuss the feel. Unfortunately, the feel of a cue made from a single piece of wood delivers the most sold feel, but because of the necessity to keep it from warping and look good this is not an option. We try to replicate the solid wood feeling as close as possible. This is done by maximizing the amount of wood-on-wood everywhere from the tip to the butt cap. I prefer wood from the shaft is glued directly to the tip without a capped ferrule. I also believe in threads in the main joint being cut directly into the wood and the use of a radial or 3/8x10 joint pin. The radial is superior because almost the thread is in contract with wood as opposed to standard threads which do not evenly distribute the contact between shaft and pin.
Secondly, to control warping, the cue is made of different types of wood, cored and joined with steel pins, which allows us to use attractive hardwoods where visible, and laminated maple where hidden under the wrap (which also looks pretty good if finished instead of wrapped). This also makes it possible to control the front to rear balance of the cue by using lighter or heaver materials in each area of the cue.
Finally, what most players ultimately care about is how good does the cue look. Sharp points have been the craze for many years, but the story of where points began is interesting. Wood was originally joined by using 4 wooden prongs instead of a tenon joint with threaded rod. The look carried over and was enhanced by adding layers of laminated colored wood for v-groove types points, stickers of points, and inlaid points. There are many ways to achieve the look of points, but they all have their roots in the old days of joining dissimilar woods with prongs.
Hopefully this helped you understand a little bit about what goes into a custom cue, and why they are a little pricey, but a good cuemaker knows how to use all these parts to achieve what we all want, the ball going into the hole and looking good while doing it!